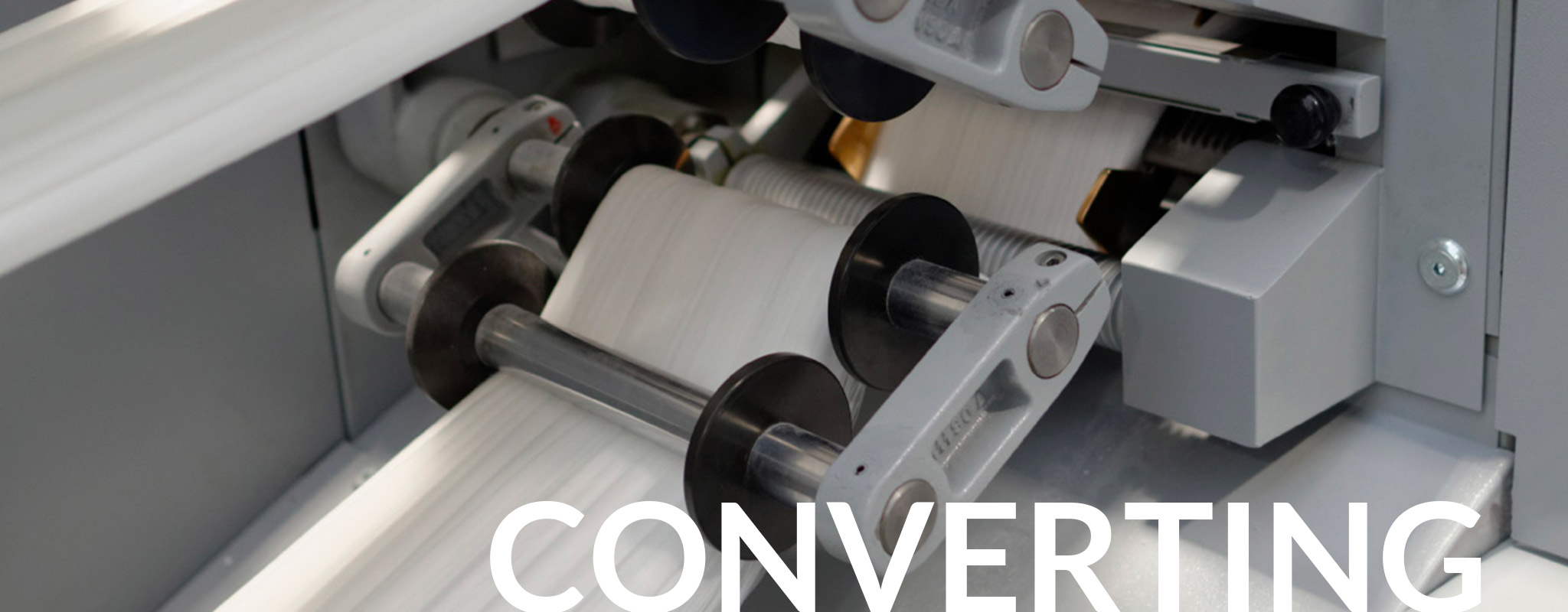
S200
The competitive stretch breaker for man-made fibres
Stretch breaking converting
The S200 stretch breaker, an essential part of the n. schlumberger Tow to Top lines, is intended for the stretch breaking of tows of chemical filaments into slivers of long fibres with a « wool type » diagram.
These slivers are essentially intended for the preparation of yarns for knitting, hosiery and hand-knitting.
The main fibres processed are acrylic (PAN), sometimes polyester (PES), polypropylene (PP) or viscose (CV).
When developing the S200 stretch breaker, the emphasis was placed on safety of use, working and quality at high speeds.
Its design and construction reflect the principles of construction and productivity on which the reputation of n. schlumberger equipment is founded. It features the following main characteristics:
Robust structure for exemplary reliability and precision
Excellent accessibility for the machine servicing and adjustments
Integral covering for a optimum operation safety
Modular construction in three identical “quadro” groups and three identical drafting groups
Heating plates with automatic control for adjusting the shrinkage ratio
Suction and cooling system on each drafting and “quadro” groups
Crimping box at delivery
Compact continuous steaming system with cooling conveyor
Feeding up to two tows (2 x 100 ktex) with safety facility in case of overloading and over tension
Man-machine dialogue at the control panel via a touch screen
The breaking on three heads with :
Pneumatic pressure on cylinders
Transmission by timing belts
Delivery speed up to 400 m/min depending on tows
The FB20 model is used in a short in-line breaking process consisting of one pre-stretching block followed by three breaking heads.
The FB20 stretch breaker converts technical fibres (flax, carbon, stainless steel)
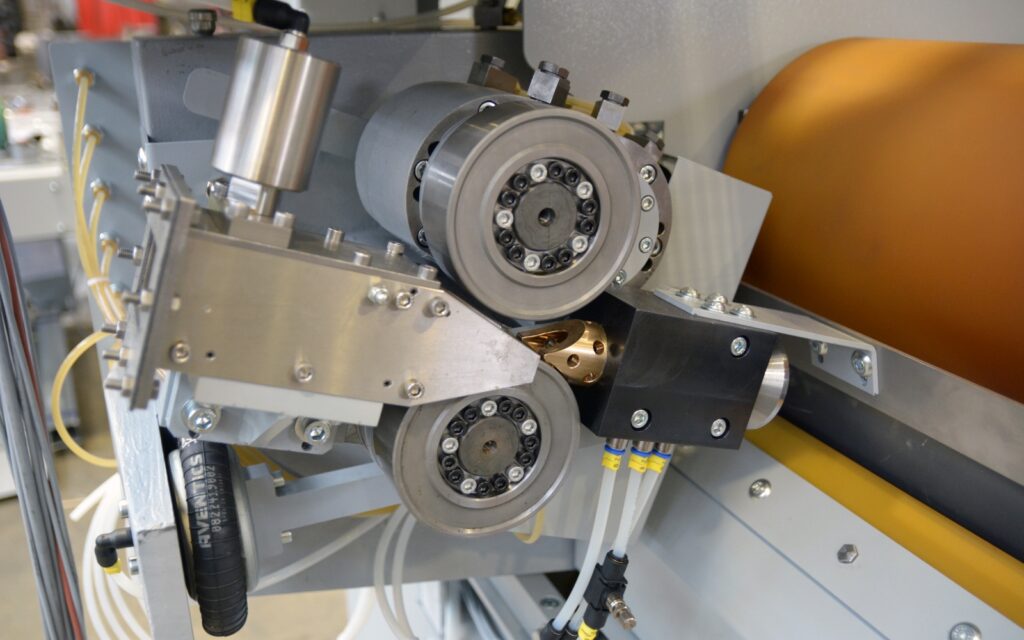

FB20
The stretch breaker for technical fibres
Stretch breaking converting
n. schlumberger also developped a short stretch breaker especially designed for technical fibres. These fibres can be carbon fibres, glass fibres, metallic fibres, para or meta-aramids fibres, polyethylen (HMPE), polytetrafluoroethylen (PTFE) but also natural fibres like flax. All these fibres are used in composites parts thanks to their exceptionnal technical characteristics (high tenacity, elongation, stiffness etc.)
The FB20 model is used in a short in-line breaking process consisting of one pre-stretching block followed by three breaking heads.
Differents options are available according to the material processed. Due to many possibilities, please contact us for more information regarding your project.
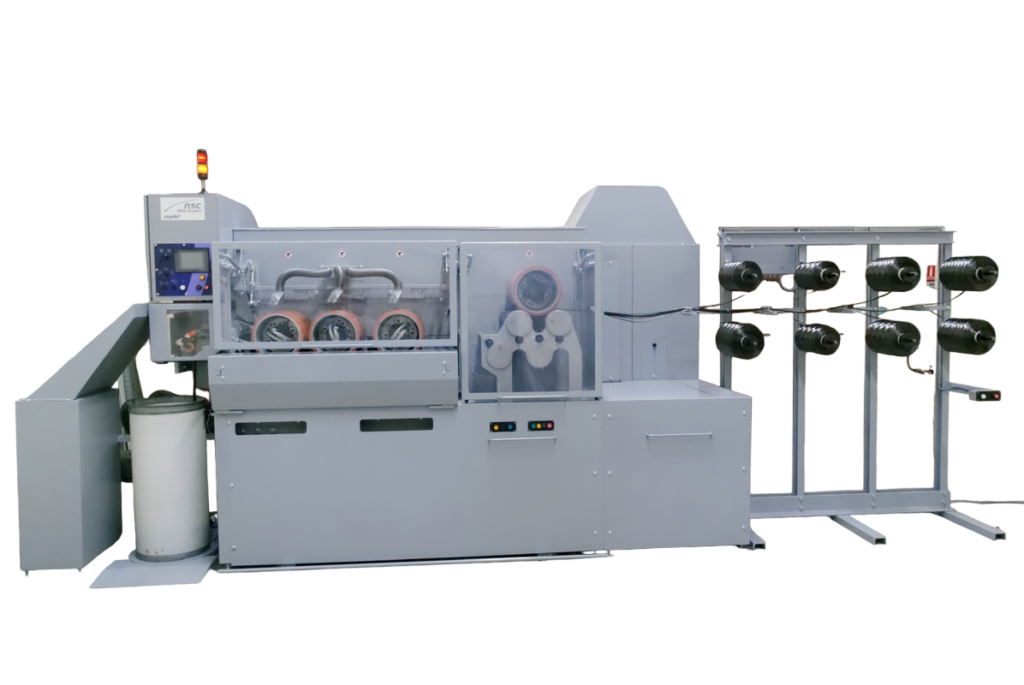


TT12
Mastering the converting of synthetic filaments
Crush cutting converting
Another essential part of our Tow to Top lines, the TT12 converter is used for crush cutting tows of synthetic filaments into slivers of fibres with a diagram similar to the wool one.
The TT12 converter is mainly for polyester (PES) but in some cases it also converts polyamide (PA) and polypropylene (PP).
This converting presents the following main advantages:
The fibres’ characteristics are maintained (crimp, resistance, lengthening)
The Hauteur diagram can easily be modified and reproduced easily
The percentages of short fibres and waste are very low.
The TT12 converter is fitted with a GC40 head and therefore benefits from the new chain gill ergonomics: better accessibility for servicing and maintenance.
Fitted with a crimping box at its delivery end, the TT12 produces a compact and resistant sliver, making it possible to increase its productivity as well as that of the next passage, and to process reputedly difficult fibres. Simple to use and safe, the TT12 converter represents the most advanced technology in terms of quality and the most efficient one from a production point of view.
The TT12 converter is fitted with a feed creel featuring detour bars and several centering devices which ensures optimum presentation of the tow in the tensioning device.
One of the converter’s major components is the cutting roller. The cutting roller, pressed against the anvil, cuts the filaments without deforming their ends. The mean height of the fibres to be obtained is determined by the cutting roller pitch (75 mm, 88 mm or 105 mm).
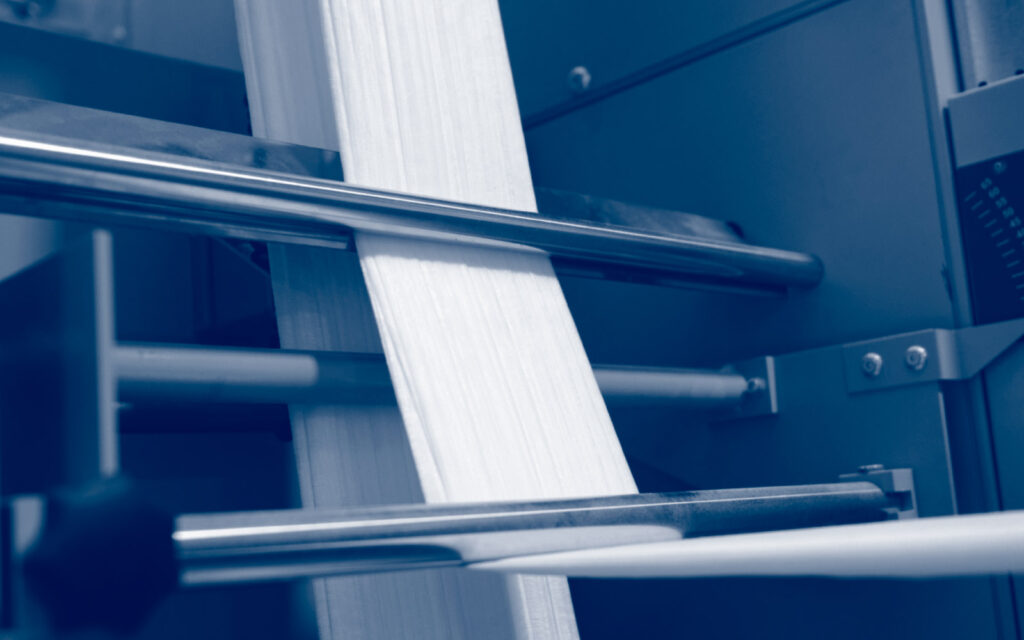
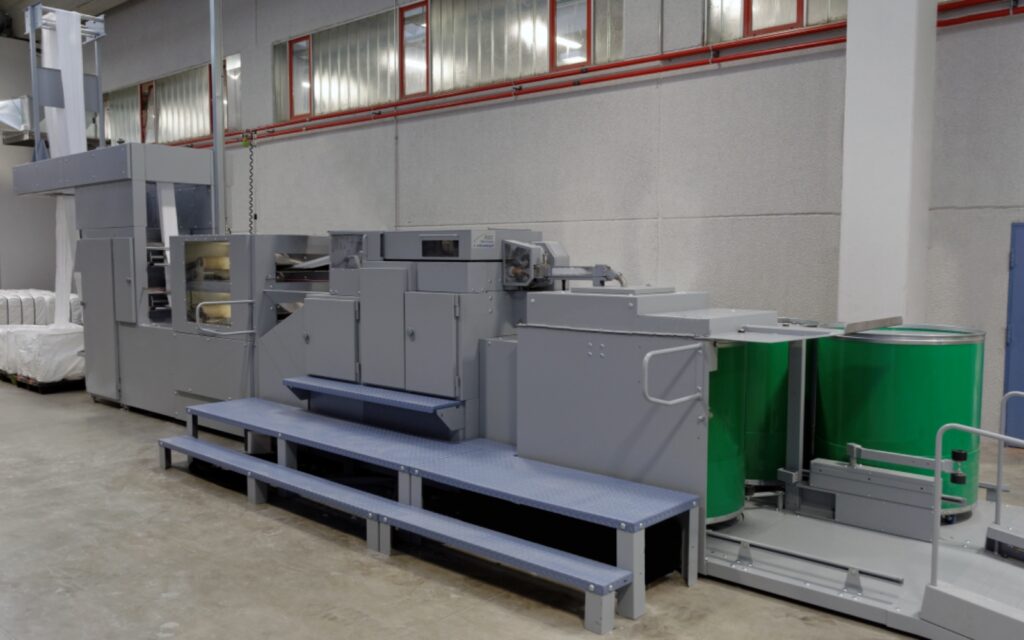